Evan Vander Stoep was a junior at Milwaukie High School when he first saw the fodder greenhouse on the farm that the agriscience class used to grow barley fodder.
“It was all in shambles, just pieced together,” he recalls. “There were parts all over the place, and it looked like it would never work.”
Although the system appeared beyond repair, Vander Stoep welcomed the challenge to get it working again. He started tinkering with the parts and sketching designs in January 2021. Even when it looked plausible on paper, agricultural education teacher and North Clackamas FFA advisor Kathy Mayfield was skeptical it could be fixed.
“My first thought was, ‘Does he really know what he’s doing?’” she says.
Feeding the Farm
The North Clackamas FFA Chapter is an urban program in Oregon. The 10-acre school farm is home to 32 producing ewes and six cows that consume more than 400 pounds of fodder per day, but the farm has a lack of acreage to grow crops and few opportunities to teach students about crop production.
Mayfield introduced controlled-environment agriculture almost a decade ago. The vertical racks allow the chapter to grow a lot of feed in a small space at a rapid pace. Her goal was to produce enough fodder to feed the livestock on the campus farm.
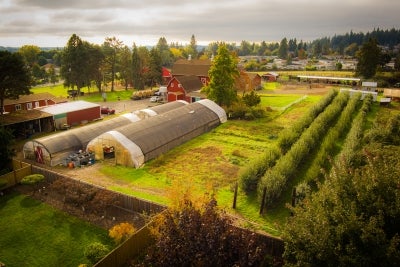
The North Clackamas FFA Chapter school farm provides multifaceted opportunities for students.
“It offers us the ability to teach kids how to produce a crop we feed to our animals,” she says. “It’s also very hands-on in terms of doing a cost analysis from an ag business standpoint, so it’s multifaceted in terms of its application.”
A 20×40-foot greenhouse on the campus farm was the ideal location to start a commercial-size barley fodder operation. Previous classes had installed a flood-and-drain system to fill trays with water that soaks the seed; these systems are common in commercial facilities but led to excess seed washout and poor production in the campus greenhouse.
In 2014, FFA members conducted an agriscience project to compare the performance of the flood-and-drain system with a mister system. The misters decreased mold levels and increased production, leading Mayfield to make the switch. However, the new system was not up and running, with most of the system torn apart when the COVID-19 pandemic shut down the operation.
When classes resumed, Vander Stoep was in the class responsible for getting the system running again after two years offline. Vander Stoep had some experience working on aquaponics and hydroponics using small fish tanks but admits, “Growing hundreds of pounds of feed per day, seven times a week, was quite a big task.”
Chris Guntermann, a greenhouse specialist, provided input on designs. The blueprints went through five revisions before Vander Stoep felt confident enough to order parts and start construction.
“Ms. Mayfield was amazing in the way she supported me,” Vander Stoep says. “She basically said, ‘I’m going to let this high schooler go and spend hundreds of dollars on plumbing and electrical parts and hope it works.’”
Concept to Completion
Vander Stoep devoted all his spare time to working on the fodder system, managing all the tasks including electrical, plumbing and writing the code for the controller. He often worked late into the evening to assemble the system and test configurations. Every day for more than four weeks, Vander Stoep traveled to the farm for the initial system trials to harvest and reseed the system himself, a two-hour daily process. He then trained other students to help run the system.
“It’s so rare that students take ownership to that level,” Mayfield says. “He didn’t just take it on to completion; he took it to a higher level than the industry standard.”
From the initial design, Vander Stoep continued making tweaks. In the original design, which he dubbed, “the spaghetti noodle disaster,” the valves that controlled the irrigation on each level of the racks were on the floor with hoses running off them.
Vander Stoep recognized it was a mess — and a tripping hazard — and switched the design so the hoses were affixed to the ceiling. The goal, he explains, was to position all the equipment so it was safe but accessible in case it needed repairs. He also made several other modifications, including programming a specialized industrial programmable logic controller (PLC) to work for the smaller-scale irrigation system to help manage the humidity in the greenhouse.
When the time came to grow fodder, Vander Stoep still had some reservations.
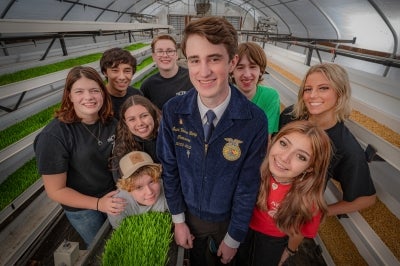
Once he improved the system, Evan Vander Stoep trained other students to help run it.
“I was confident the plumbing and electrical were going to work,” he says. “but I wasn’t sure I could hit the production goals Mayfield wanted to hit.”
Mayfield challenged Vander Stoep to optimize the moisture levels, temperature and humidity to produce 7 pounds of fodder per pound of seed, but the initial results were disappointing.
The irrigation controller and climate control settings Vander Stoep initially spent days refining produced a volume of fodder as low as 3.2 pounds per pound of seed, which was barely enough to feed six cows. Vander Stoep was undeterred.
“Electronics have always been my passion,” he says. “I like being hands-on and working on stuff, and it’s amazing to work on these things I would never have the ability to do if it wasn’t for FFA.”
With continued tweaks (coupled with a stubborn refusal to give up), Vander Stoep started seeing improvements in production. He quickly decided to turn his experimentation into an agriscience project.
Seed Germination Science
Before each batch of fodder is started, four 15-pound bags of seed are soaked in 5-gallon buckets with water and an ounce of bleach for 24 hours. Vander Stoep wondered whether the water temperature during the seed priming presoak affected the ending production weights.
To test the impact, Vander Stoep filled two of the buckets with regular hose water of about 50 degrees Fahrenheit and used a 300-watt aquarium heater to control the temperature of the water in two other buckets, changing the temperature to collect data on the impact of a wide temperature range. The 15-pound bags of seed would then be lowered into the four buckets of water and left to soak for 24 hours.
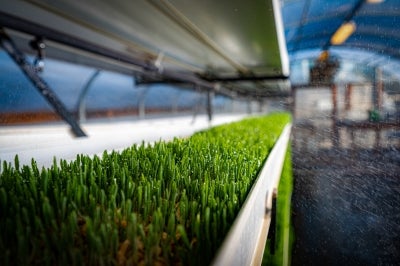
Before fodder can be harvested, the barley is placed in a presoak treatment and undergoes several growth stages.
It didn’t take long to see a clear pattern of the impact the water temperature during the presoak had on production (based on harvested weight) once the seed was planted.
“I noticed there was a peak in production weights when the seed was soaked in water in the 72- to 75-degree range,” Vander Stoep says. “Temperatures above 80 degrees were way too high. At those high temperatures, [the seed] started degrading and production levels were sometimes below normal.”
Vander Stoep suspects the warm presoak better penetrates the seed, allowing it to hold more water and provide a boost during sprouting. The findings could help the North Clackamas FFA Chapter produce an extra 40 pounds of fodder per day, therefore feeding more animals.
The project earned Vander Stoep first place in the Oregon Agriscience Fair and a spot as a 2023 National FFA Agriscience Fair finalist.
Taking the Next Step
Vander Stoep graduated in 2023 and accepted a position as a radio tower technician. He travels around the country repairing and installing technical equipment, which sometimes requires climbing hundreds of feet into the air to work on the tower’s antennas and lights.
Similar to redesigning the irrigation system for the barley fodder operation, repairing radio towers requires top-notch technical and problem-solving skills. Vander Stoep is enjoying traveling to different states for work but hopes to return to agriculture in the future.
“I have a creative side; I like to come up with new ideas and design custom components,” he says. “I want to put those passions to use and continue down an agricultural path; it’s something I’m interested in and passionate about.”